Choosing the right DTF machine can revolutionize your printing endeavors. But, which DTF machine stands out for its print quality, versatility, and value in 2024? This guide provides answers, showcasing top performers and helping you pinpoint which DTF printer aligns with your production needs.
Key Takeaways
- DTF printers are a revolutionary technology in the garment printing industry, known for their ability to produce vibrant and durable prints on various fabrics without pretreatment.
- Choosing a DTF printer involves considering factors like print quality, speed, print head design, and software compatibility. DTF machines range from high-end printers with outstanding quality to entry-level models that provide cost-efficiency and ease of use.
Despite the challenges of maintaining DTF printers and ensuring consistent ink flow and transfer quality, their advantages over other printing technologies like DTG and screen printing make them a valuable asset for any textile printing company.
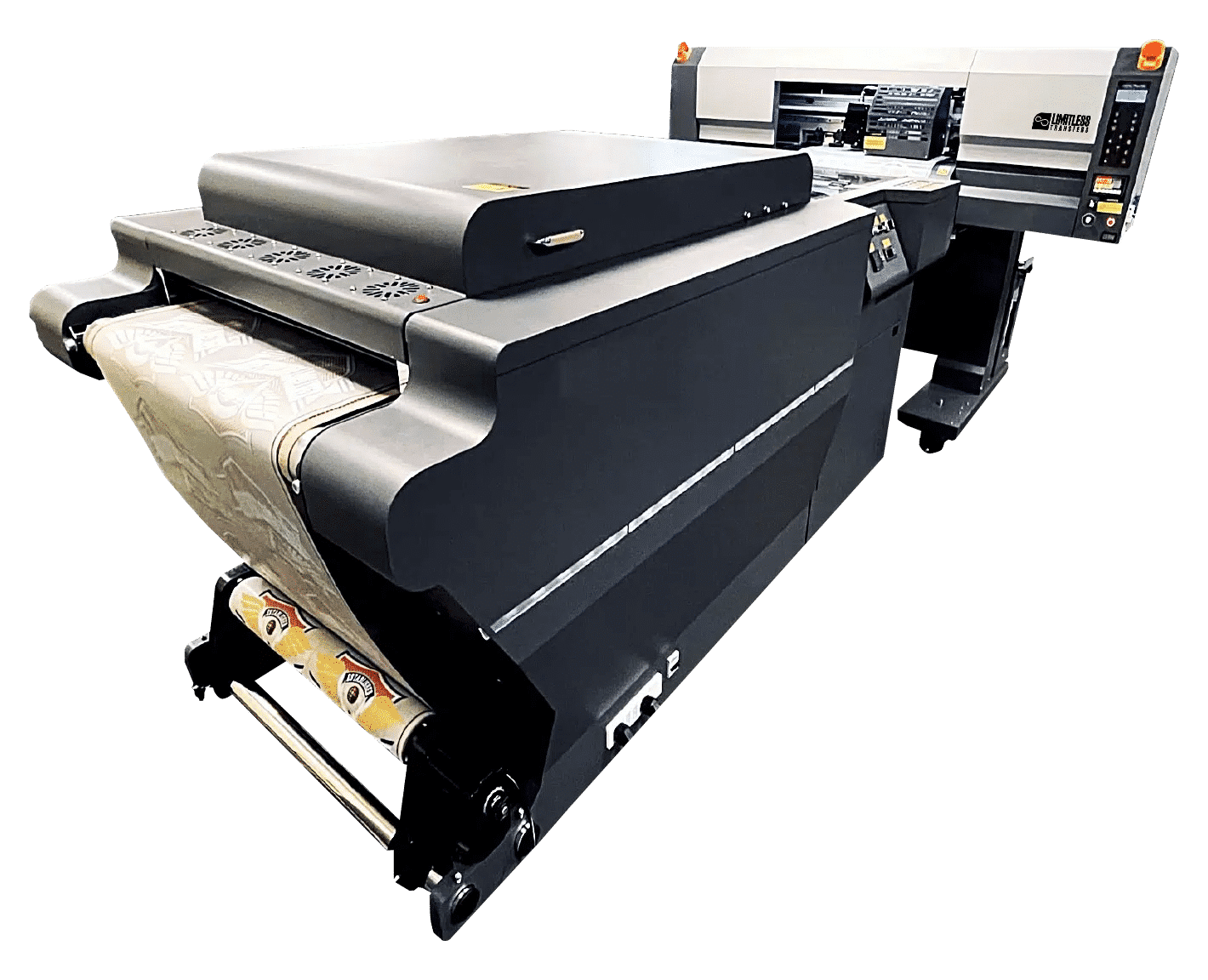
Understanding DTF Machines
DTF machines, also known as DTF transfer printers, have emerged as a game-changer in the printing industry. With their unique powder-shaking function and ability to produce top-tier prints, a DTF transfer printer sets itself apart. These machines utilize distinctive pigments in their inks, including a white ink under base. The top-quality inks and powders used in DTF transfer printing allow your creations to stand out in the ever-growing decorated apparel industry.
What is a DTF Machine?
The vibrant visuals of a DTF transfer design are meticulously crafted through the use of RIP software and a DTF transfer printer. This process involves the strategic layering of white ink and an array of colored inks onto PET transfer film, followed by the application of DTF powders.
This intricate methodology breathes life into the design, transforming it from a simple idea into a tangible, dynamic piece of art. Known for its superior image quality, DTF printing renders intricate designs with sharp lines, vibrant hues, and impressive longevity. The DTF transfer film can be applied to both small and large print surfaces, representing a cutting-edge advancement in DTF printer work and apparel printing.
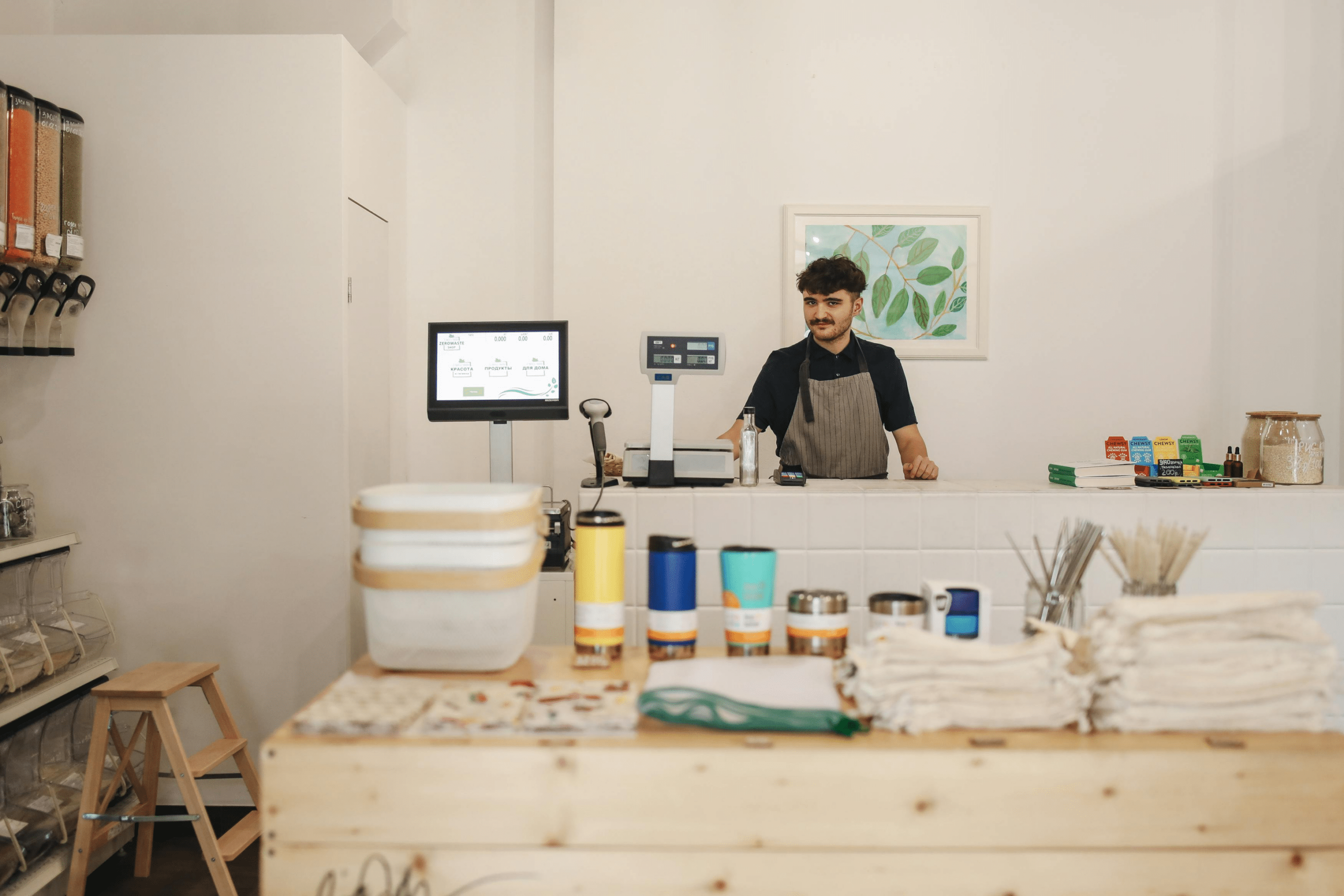
Advantages of Utilizing DTF printers for Businesses are Manifold. They Allow for:
- The hassle-free production of high-quality and durable custom DTF transfer prints
- The elimination of the need for pretreatment
- Enables businesses to offer their services at competitive prices.
- Ability to comfortably print on difficult fabrics, such as polyester, spandex, and nylon materials
- Enables businesses to offer their services at competitive prices.
The Benefits of DTF Printing Include:
- More durable prints compared to other printing methods
- Ability to produce precise and intricate designs
- Cost-effective pricing for small to large-sized orders
- Utilization of eco-friendly inks
Common Applications for DTF Printing
DTF printing is used extensively, from transferring images and artwork onto fabric such as clothing and athletic jerseys to printing in the fashion industry for custom apparel. The primary products typically manufactured through DTF printing, a form of textile printing, include t-shirts, pockets on hoodies or shirts, hats, and pants.
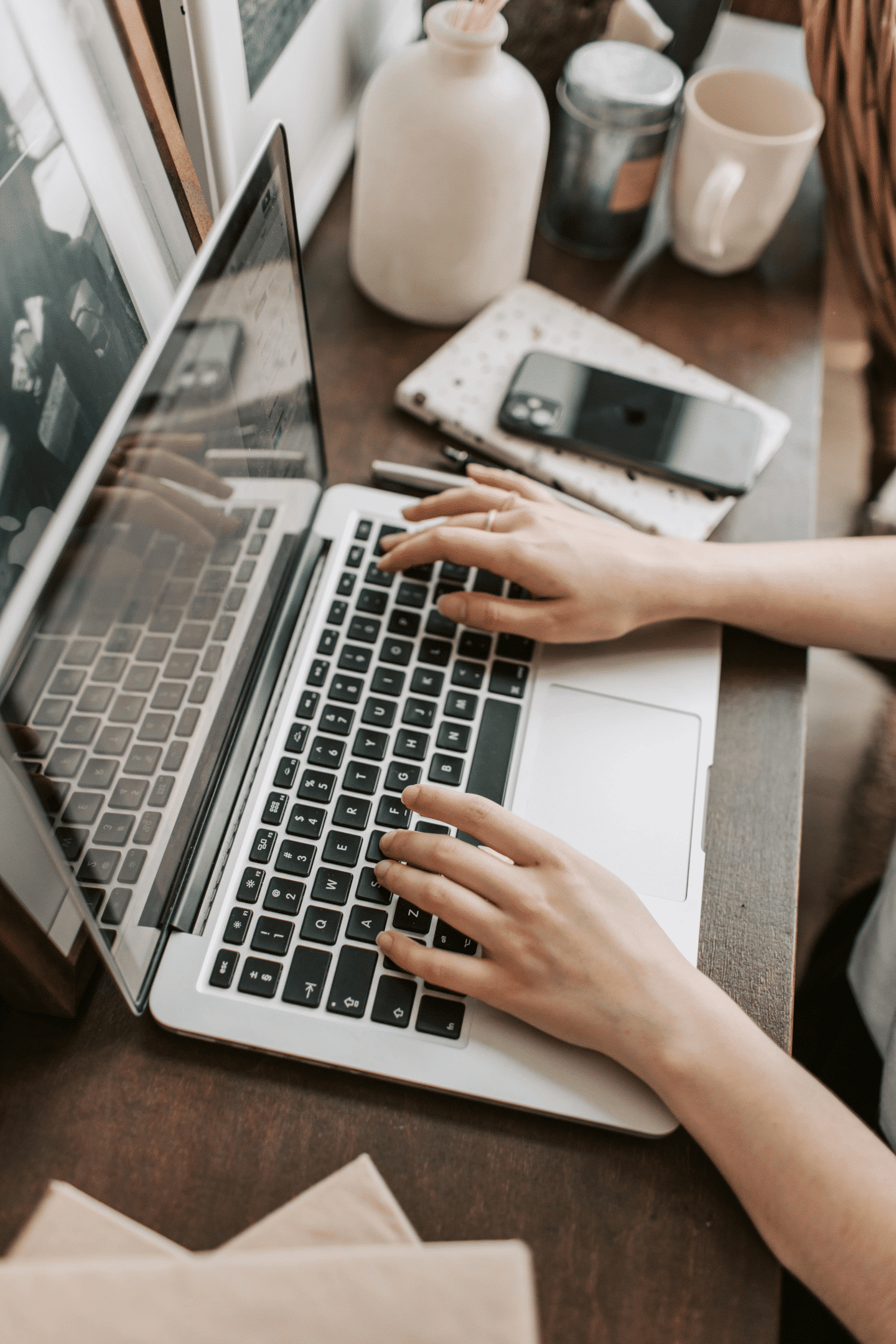
Top DTF Printers on the Market
The market is filled with a plethora of DTF printers, each with their unique features and benefits. The high-end models offer features such as high-resolution printing, industrial-print-quality output, and compatibility with multiple fabric types, making them ideal for producing DTF transfers.
Mid-range DTF printers provide essential elements such as advanced printheads, quality DTF supplies, competitive pricing, cost-efficient operation, as well as reliable support and service. Their specifications enable direct ink application, flexibility in material and color printing, and long-lasting durability.
High-End DTF Printers
High-end DTF printers are renowned for their ability to produce top-notch, vivid prints with exceptional longevity. They incorporate cutting-edge technology and innovative features to guarantee superior print quality. They also offer:
- Extensive material compatibility
- Elimination of the need for pretreatment
- Fast and efficient production of DTF transfers
- Prints that surpass DTG prints in durability
Mid-Range DTF Printers
For those seeking a balance between cost and performance, a mid-range DTF printer, like the Xinflying X5+ DTF printer, is an excellent option. This printer offers a blend of essential features that meet market demand, while providing cost-efficient operation and reliable support and service.
Entry-Level DTF Printers
For small businesses or startups, entry-level DTF printers like the Epson SureColor F570 and the A4 DTF Printer priced just under $2000 provide an affordable entry point. Despite their lower price point, these printers don’t skimp on performance, delivering vibrant prints on a variety of materials.
These printers also take into account the need for cost-efficient operation and user-friendly design, making them a great starting point for those new to the industry.
Key Features to Consider When Choosing a DTF Printer
Selecting a DTF printer calls for careful attention to key features that significantly influence your printing outcomes. These include print quality and speed, print head design and technology, and software compatibility and ease of use. Understanding these features will ensure you select a DTF printer that aligns with your business needs and operational demands.
Print Quality and Speed
The interplay between print quality and speed plays a key role in determining the performance of a DTF printer. While increased print speeds can improve productivity and save time, it is vital to maintain a balance with the printer’s capability to uphold high-quality prints for meeting standards. Therefore, the ability to adjust print speed and quality according to your specific needs is a key feature to look for in a DTF printer.
Print Head Design and Technology
The print head’s role in a DTF printer’s performance is crucial because it ensures precise ink delivery onto the film. A high-quality print head is vital for achieving vibrant and precise prints in DTF printing. Any issues such as clogging or burning of the print head can significantly affect the machine’s overall operational status.
Software Compatibility and Ease of Use
When selecting a DTF printer, the ease of use and software compatibility should be prioritized. The RIP software should seamlessly integrate into your existing workflows and systems, leading to an efficient printing process and minimizing operational challenges.
It should also provide a user-friendly interface that allows easy navigation and utilization.
The DTF Printing Process: Step-by-Step
The DTF printing process is a meticulous yet straightforward procedure involving a series of steps from design preparation to heat pressing. Understanding each step will enable you to achieve optimal results and improve your printing efficiency.
Creating Digital Transfer Sheets
Creating brilliant digital transfer sheets is the first step in the DTF printing process. It involves:
- Printing the design onto a specialized film using pigment ink
- This ink contains solid pigment particles in a liquid carrier
- The ink is used due to its quality, durability, and compatibility with the DTF process, offering an alternative to traditional screen printing.
Applying Adhesive and Powder
The next step in the DTF printing process is the application of adhesive powder. The adhesive powder is evenly applied to the wet ink on the film, after which any excess powder is removed, ensuring that adhesive remains only on the printed areas. This process prepares the print for the subsequent transfer onto a garment.
Heat Pressing and Finishing
The final step in the DTF printing process is heat pressing and finishing. The process involves the following steps:
- Place the printed film onto the fabric.
- Use a heat press machine to apply heat and pressure to the film and fabric.
- The heat and pressure activate the adhesive powder on the film.
- The adhesive powder bonds with the fabric, transferring the design.
After the heat pressing process, the film is carefully peeled off, leaving the design on the fabric. For optimal results, employ a high-quality heat press. Visit our website to browse through the best heat press options on the market.
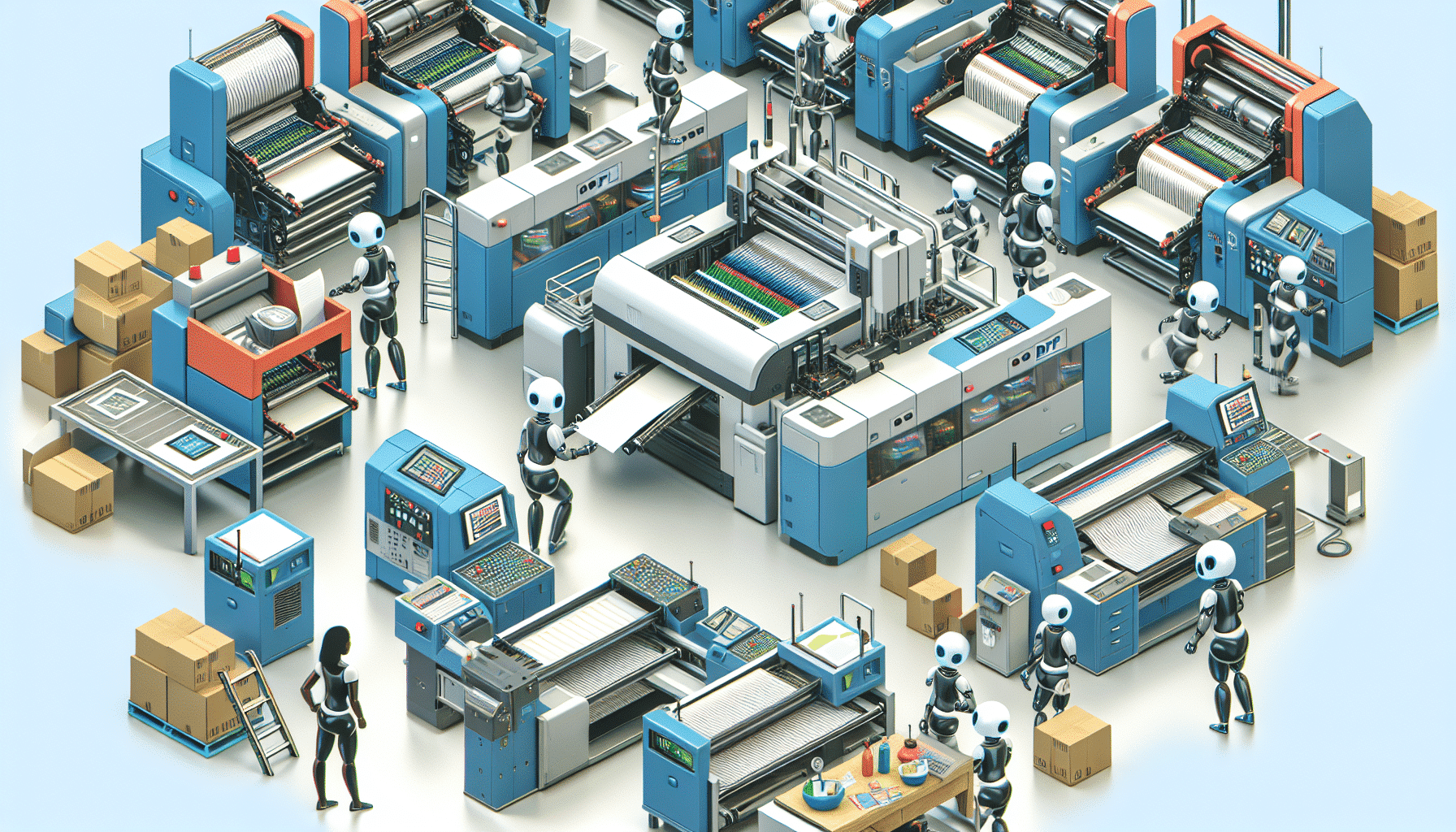
Tips for Optimizing Your DTF Printing Workflow
You can ensure a seamless DTF printing process by implementing strategies that streamline your workflow. This includes proper maintenance and cleaning of your DTF printer, employing effective pre-press techniques, and taking measures to maximize output and reduce waste.
Proper Maintenance and Cleaning
Performing regular maintenance on your DTF printer can help you avoid common issues like print head clogs and ensure that your printer continues to produce high-quality prints. Here are the steps to follow:
- Remove the carriage.
- Utilize a non-woven cloth soaked in a cleaning solution to wipe the printhead and eliminate any ink residue.
- Clean the external components with a lint-free cloth.
- Delicately blot the capping station with a DTF cleaning solution.
By following these steps, you can keep your DTF printer in optimal condition.
Effective Pre-Press Techniques
Effective pre-press techniques can significantly improve the quality of your DTF prints. These include:
- Pre-pressing garments to remove moisture and wrinkles
- Calibrating the printer for color uniformity
- Using gloves to prevent oil and dirt transfer to the film
- Handling the film with care to prevent creases and folds.
Maximizing Output and Reducing Waste
Improving the efficiency of your DTF printing workflow hinges on maximizing output and minimizing waste. This can be achieved by:
- Effectively managing ink usage through regular monitoring and replenishment
- Leveraging the sustainability advantages of DTF printing, such as the use of water-based inks, to minimize waste
- Recycling DTF powder shakers instead of disposing of them after a single use.
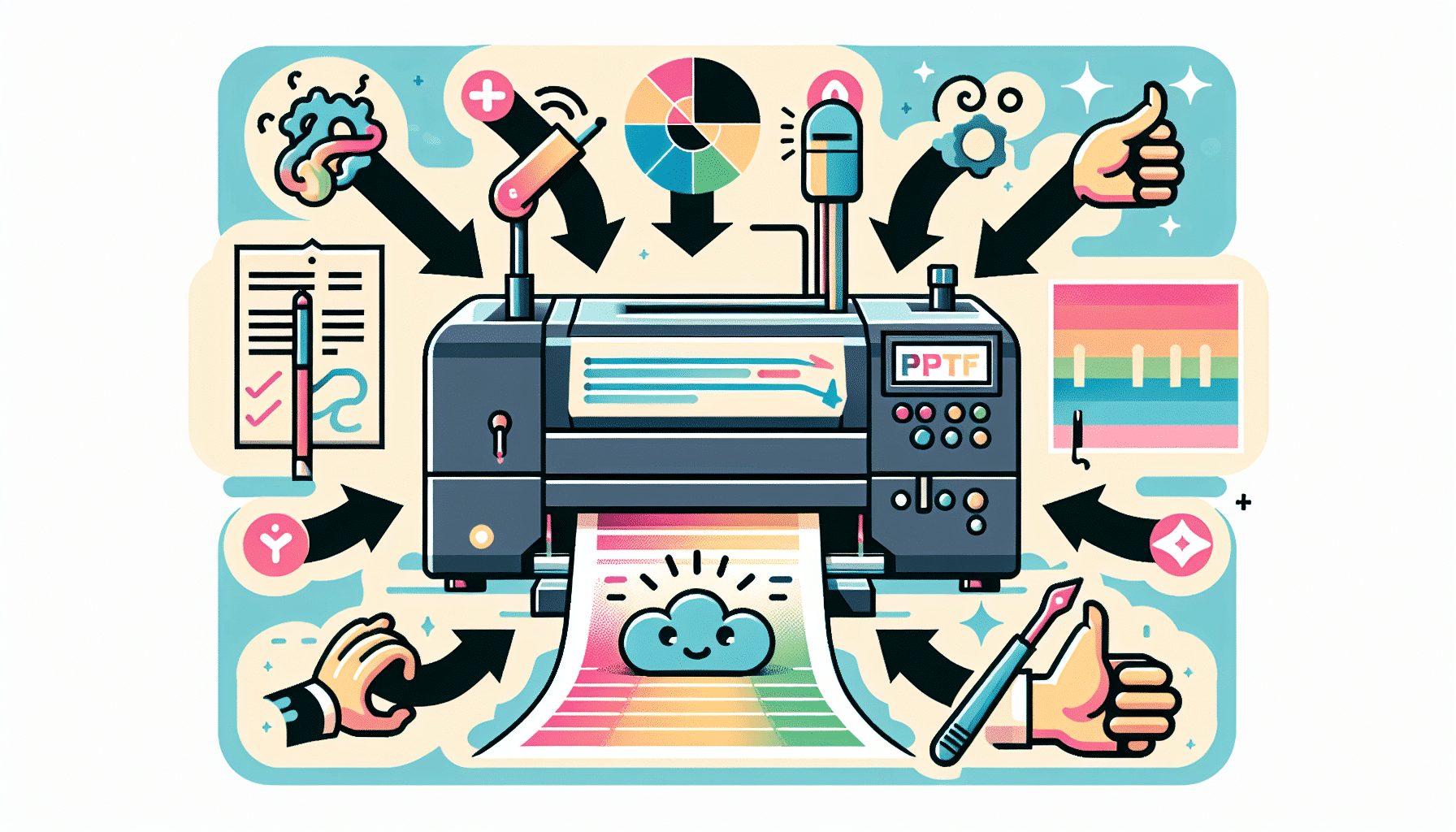
DTF Machine Printing Challenges and Solutions
DTF printing, like any technology, presents its unique set of challenges. However, understanding these challenges and knowing how to overcome them can ensure that your DTF printing operations run smoothly.
Ensuring Consistent Ink Flow with a DTF Machine
Maintaining print quality requires a consistent ink flow. This can be achieved by regularly cleaning the printheads, ensuring a stable power supply, and controlling the temperature and humidity levels in the printing environment.
Achieving Optimal Transfer Characteristics
Producing high-quality DTF prints necessitates the achievement of optimal transfer characteristics in the direct to film process. This involves:
- Using high-quality ink to produce prints with vibrant colors and a premium appearance
- Selecting the appropriate film
- Adhering to the sequential process of printing on the film and directly transferring onto fabric
Comparing DTF with Other Printing Technologies
Comparing DTF printing with other popular printing technologies, such as screen printing, offers deeper insights into its distinct advantages and potential uses.
DTF vs. DTG
DTG printing, also known as direct-to-garment printing, employs specialized aqueous inkjet technology to print on textiles, making it well-suited for intricate, multi-color designs on products like t-shirts and hoodies.
On the other hand, DTF offers significant advantages over DTG, such as:
- Its ability to print on a wide variety of fabrics with exceptional durability
- The printed designs can withstand stretching without cracking or peeling
- They retain their vibrancy even on dark-colored garments
DTF Machine Printing vs. Screen Printing
Comparing DTF machine printing to traditional screen printing methods can further highlight the advantages of DTF. While screen printing has long been lauded for its cost-effectiveness, direct to film printing brings several compelling advantages to the table.
Notably, it boasts the capability to print and chemically bond with a diverse range of materials, extending to dark and textured fabrics. Moreover, DTF printing significantly accelerates the printing process, particularly for small orders at automatic screen print shops using film printers.
Summary
DTF printing technology has revolutionized the printing industry, offering a versatile, efficient, and high-quality solution for a wide range of applications. From the creation of vibrant, long-lasting prints to its cost-effectiveness, DTF printers have proven to be a game-changer in the world of printing. Whether you’re a small business owner looking to expand your product offerings or a large manufacturer seeking to improve efficiency and output, adopting DTF printing technology can provide a significant boost to your operations. To learn more about the DTF printing technique, visit LimitlessTransfers.com.