The allure of heat transfers and fabric printing is as timeless as it is ubiquitous. From the subtle branding on clothing to the striking advertising on banners, the versatility and widespread application of fabric printing make it an art and a technical science simultaneously. One of the most innovative methods in the world of fabric printing is the rising star, Direct to Film (DTF) printing—a digital technology that combines versatility, vibrancy, and hardiness. Understanding the nuances of heat transfer in DTF printing is to unlock a trove of possibilities for businesses and artists alike.
In this comprehensive guide, we’ll explore the intricate dance of heat and ink, demystifying the principles that underpin DTF printing. Whether you’re a fledgling entrepreneur on the cusp of venturing into DTF, a seasoned fabric printing professional looking to expand your repertoire, or simply a curious mind, join us as we peel back the layers of this cutting-edge process.
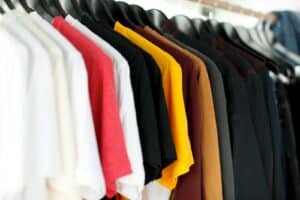
Section 1: Unveiling DTF Transfers: Heat Transfers
The Basics of DTF Printing
DTF printing is a method that allows digital image files to be directly printed onto a variety of fabrics using specialized printers and inkjet technology. In contrast to the more traditional methods, like screen printing and heat transfer vinyl, DTF offers greater detail, color vibrancy, and print longevity. Each color in the design is printed separately onto a clear polyester film base and then transferred to the fabric.
Understanding the DTF Printing Process
DTF printing is a multi-step process that involves preparing the film, printing the ink, and transferring the design to the fabric.
-
Film Preparation: A clear, heat-resistant DTF film is treated and cured to ensure it can properly accept and retain the ink.
-
Ink Application: Specialized DTF inks are used in the printing process. These inks are designed to adhere to the film and fabric during the transfer process.
-
Curing: The printed film is cured using heat to ensure that the ink bonds with the fabric effectively.
-
Foam Lamination: The fabric and printed film undergo a process to add a layer of foam for texture and to enhance print quality.
-
Heat Press Transfer: The DTF film is then pressed onto the fabric using a heat press machine. The heat and pressure enable the ink to transfer to the fabric, completing the print.
Section 2: The Role of Heat in DTF Printing: Heat Transfers
How Heat Affects DTF Film
In DTF printing, heat is a defining factor in the transfer of ink from the film to the fabric. It has several crucial roles:
-
Curing the ink to the film, ensuring it is dry and ready for transfer without smudging.
-
Heat activates the adhesive properties in the film, allowing it to bond with the fabric.
-
It softens the ink, allowing it to penetrate the fabric fibers more effectively for a long-lasting print.
The Process of Curing
Curing is the transformation of ink from a liquid or semi-liquid state to a solid through the application of heat. In DTF, curing is typically the first step after ink application, ensuring that each layer of ink is thoroughly dry before the next layer is applied.
Heat Press Vs. Curing Ovens
Traditionally, curing ovens were used in DTF printing, but modern technology has given rise to heat press machines that combine curing and transfer steps in one. These machines apply heat and pressure directly, offering a more controlled and streamlined process.
Tips for Optimal Custom Heat Transfers
To achieve the best results in DTF printing, the following tips are invaluable:
-
Consistent and Appropriate Temperature: Uniform heat across the entire plate of the heat press is critical to a successful transfer.
-
Pressure and Time: Both the pressure exerted and the duration the fabric and DTF film are under the heat press are crucial. Over-pressing can distort the image, while under-pressing may result in a suboptimal transfer.
-
Cooling Time: After the transfer, cooling the fabric under a set duration helps set the ink and improve the final print’s durability.
Section 3: Ink Types and Heat Tolerance: Heat Transfers
The Importance of the Right Ink
Not all inks are created equal. The success of DTF printing relies on using inks formulated specifically for the heat and pressure of the transfer process. DTF inks need to be heat-resistant, durable, and vibrant, making them well-suited for a wide range of fabrics.
Heat-Resistant Inks and Their Composition
DTF inks are typically composed of a mixture of pigments, binders, and carriers designed to tolerate the curing process and subsequent transfer process without degradation. They may also contain additives to increase wash fastness and UV stability once transferred to the fabric.
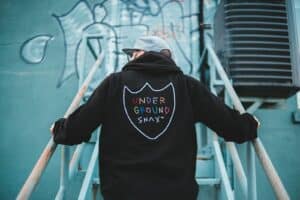
Section 4: Temperature and Fabric Selection: Heat Transfers
Fabric Selection for DTF Heat Transfer
The choice of fabric has a significant impact on the heat transfer process. Natural fibers like cotton and silk require lower temperatures and shorter heat press durations compared to synthetic fibers. DTF printing can be successfully performed on a variety of fabrics, including:
-
Cotton
-
Polyester
-
Lycra
-
Cupro
-
Spandex and more
Recommended Heat Settings for Different Fabrics
-
Cotton: A heat press set to 160-180°C (320-356°F) for 20-25 seconds
-
Polyester: A heat press set to 140-150°C (284-302°F) for 15-20 seconds
It is crucial to test the heat transfer settings on a small sample of fabric before undertaking a full production run to ensure the best results. The fabric blend, color, and weight all play a role in the final temperature and duration required for a successful transfer.
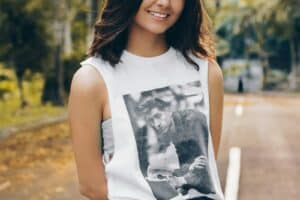
Section 5: Heat Transfers: Issues and Solutions
Understanding and Resolving Adhesion Problems
Proper adhesion is essential for a high-quality DTF print. Issues such as incomplete transfers, peeling, and ghosting can be due to:
-
Low heat press temperature
-
Inadequate pressure
-
Improperly cured ink
Solutions include increasing temperature, applying firmer pressure, and verifying the curing process to ensure the ink is fully bonded to the film before transfer.
Dealing with Over-Heating
Overheating can cause the ink to spread uncontrollably or the fabric to scorch. It is important to monitor the heat press temperature and use the recommended settings for the chosen fabric. If overheating occurs, reducing pressure and duration may help mitigate the issue.
Ensuring Even Distribution of Heat and Pressure
An uneven application of heat or pressure can result in an inconsistent or distorted print. A heat press with adjustable settings offers the flexibility to fine-tune these parameters. Additionally, using a test patch before the full transfer can help identify any issues and make necessary adjustments.
Section 6: Advantages and Applications of DTF Printing
The Advantages of DTF Printing
DTF printing offers numerous advantages over traditional fabric printing methods:
-
High resolution and detailed prints
-
Excellent color vibrancy and saturation
-
Durability, especially with wash-resistant inks
-
Shorter setup and cleanup times compared to screen printed times.
-
The ability to print small runs cost-effectively
-
A more environmentally friendly approach with reduced chemical usage
Applications of DTF Printing
The versatility of DTF printing opens doors to various applications, including:
-
Custom apparel and fashion
-
Promotional products
-
Soft signage and banners
-
Interior decorations
-
Sporting goods and uniforms
Section 7: The Future of Heat Transfer in Fabric Printing
Innovations and Technologies Shaping the Future
The future of DTF printing is marked by ongoing innovations, including:
-
Development of more eco-friendly inks and curing processes
-
Advancements in heat press technology to further streamline and control the transfer process
-
Integration with other digital printing technologies for a more seamless production line
The Eco-Friendly Imperative
The fabric printing industry is increasingly turning towards eco-friendly practices. The ability of DTF printing to reduce water consumption and waste, coupled with the development of greener inks, positions it at the forefront of sustainable printing methods.
Section 8: Tips for Launching Your DTF Transfer Journey: Heat Transfers
Investing in the Right Equipment
To excel in DTF printing, investing in quality equipment is non-negotiable. This includes a reliable DTF printer, curing equipment or heat press, and, importantly, a well-ventilated and safe working environment.
The Art of Perfecting Your Technique
Mastery of the DTF process is a multi-faceted endeavor. Study the intricacies of each step, from film preparation to finishing touches, and continuously refine your techniques to ensure flawless prints every time.
Building a Strong Network
Networking with suppliers, industry peers, and potential customers can provide valuable insights and support. Stay connected with the DTF community to keep abreast of industry trends and innovations.
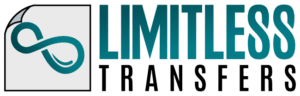
Heat Transfers: DTF Printing at the Heart of Fabric Innovation
DTF printing stands as a wonderful marriage between artistry and technology. With a detailed understanding of the role of heat in the process, the potential is boundless. Whether your aim is to produce vibrant, intricate designs on textiles or revolutionize your brand’s merchandise, DTF printing holds the key to unlocking a world of opportunities.
By staying informed, investing in high-quality equipment, and cultivating strong industry relationships, you’re poised to make a significant mark in the dynamic world of DTF printing. Welcome to the forefront of fabric innovation, where heat is not just a necessity but a catalyst for transformation
Limitless Transfers provides the best heat transfer and DTF printing services!