Struggling with your heat press settings? Our heat press guide simplifies the process by providing clear temperature and time settings for materials like HTV, sublimation, and DTF printing. Discover how to achieve perfect transfers and professional-quality results.
Key Takeaways
-
Understanding the right temperature, time, and pressure settings is crucial for effective heat press applications, whether for HTV, sublimation, or DTF printing.
-
Preheating materials and using protective sheets like Teflon or parchment paper can enhance the quality of transfers and prevent common issues.
-
Limitless Transfers offers high-quality DTF printing with quick turnaround and no setup fees, making it easier for businesses to start their heat press projects.
The Best Heat Press Guide: Essential Temperature and Time Settings
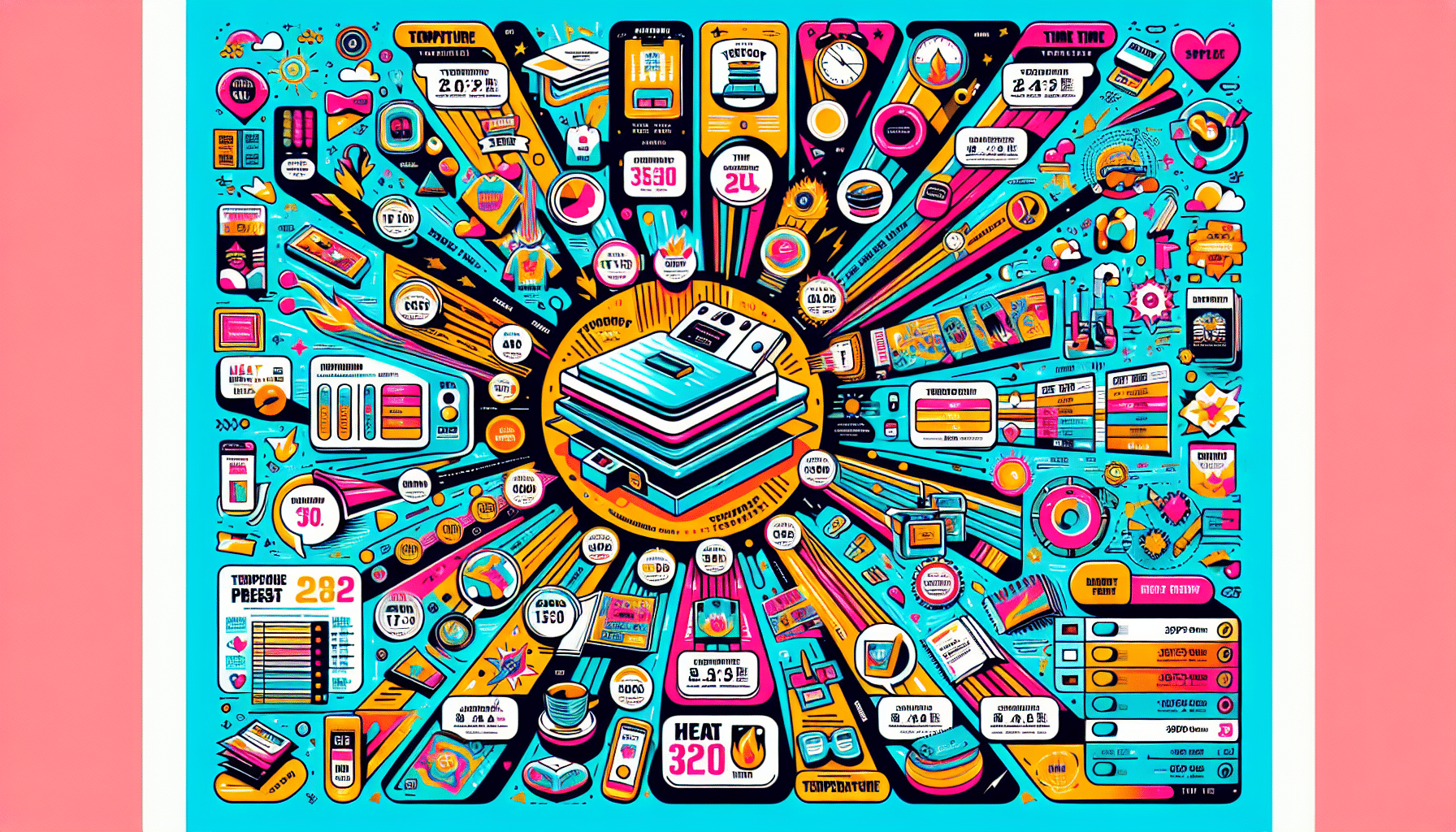
A well-rounded heat press guide is invaluable for anyone in customization. Often, users are left struggling due to a lack of comprehensive resources. This guide addresses that, offering detailed settings for various methods—from heat transfer vinyl (HTV) to sublimation printing and direct-to-film (DTF) printing.
Heat presses are essential tools in the customization industry, applying the necessary heat and pressure for effective transfers through the printing process of heat press printing. Our guide will help you maximize efficiency and achieve high-quality results, no matter your application. Say goodbye to guesswork and hello to flawless prints!
Introduction
In customization, a reliable heat press guide is indispensable. Whether starting out or running a business, understanding heat, pressure, and temperature settings is crucial. This guide covers dye-sublimation, DTF, HTV, laser transfer paper, and screen-printed transfers to ensure top-notch results.
Start by powering on the heat press and letting it reach the target temperature. The screen displays relevant information, making it easier to adjust settings based on your material and design needs. Preheating materials to remove moisture or wrinkles ensures a smooth transfer.
Key Applications of Heat Press Machines
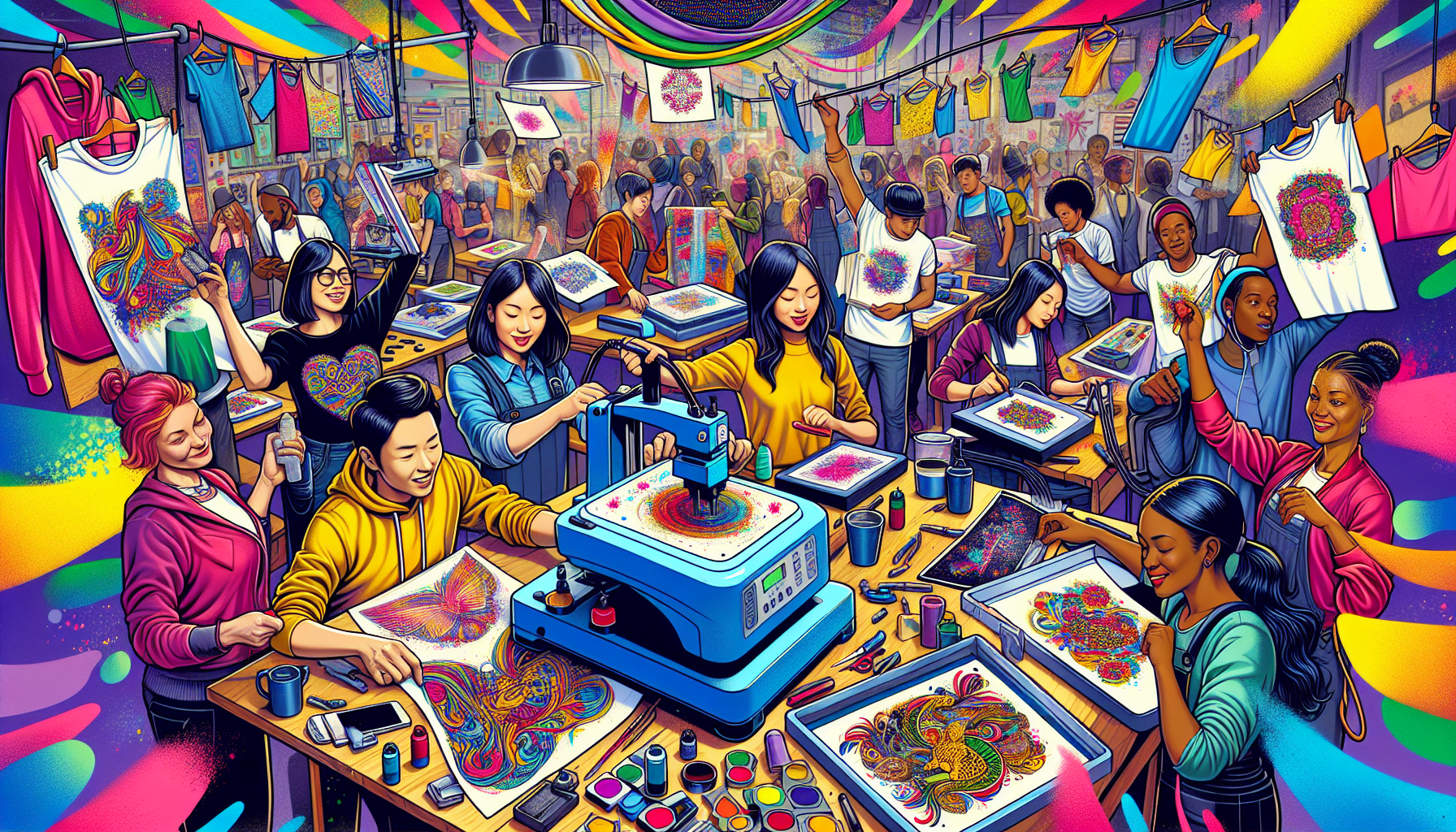
Heat press machines are versatile tools for various customization techniques, applying consistent heat and pressure for effective transfers. Key applications include heat transfer vinyl, heat press vinyl, Sublimation Printing, and Direct-to-Film (DTF) Printing.
Each application has unique requirements and benefits. From custom t-shirts to intricate designs on synthetic fabrics, mastering specific settings ensures high-quality results.
Explore each key application in detail to achieve optimal results with your heat press.
Heat Transfer Vinyl (HTV)
Heat Transfer Vinyl (HTV) is a popular choice for customizing t-shirts and other fabric items. The heat press ensures consistent heat and pressure application, which is crucial for bonding HTV with fabric. Recommended temperatures for HTV vary by brand and fabric type.
Ideal heat press settings for HTV depend on the HTV type, fabric type, and heat press model. Use a vinyl cutter for designs and test settings on a sample project to avoid costly mistakes. A clean shirt is essential to prevent oils and grime from ruining the transfer.
Lighter fabrics require lighter pressure; medium pressure is advised for most applications. Peel HTV glitter while warm for a clean release. Use equations to determine timer settings if unsure about the duration.
Sublimation Printing
Sublimation printing requires specific substrates, mainly polyester-based fabrics or polymer-coated surfaces. This process involves transferring designs onto compatible substrates and needs extra heat compared to other techniques.
In sublimation printing, inks change from solid to gas, bonding with the substrate. This ensures vibrant and durable prints, ideal for light fabrics and synthetic materials.
Direct-to-Film (DTF) Printing
Direct-to-Film (DTF) printing focuses on garment customization, including t-shirts, hoodies, and other apparel. It involves melting adhesive powder to bind prints with fabric, ensuring a strong bond.
Factors influencing DTF printing outcomes include fabric thickness, base color, and design size. Practice runs and allowing fabric to cool between presses can improve adhesion and print quality.
Understanding Heat Press Machine Settings
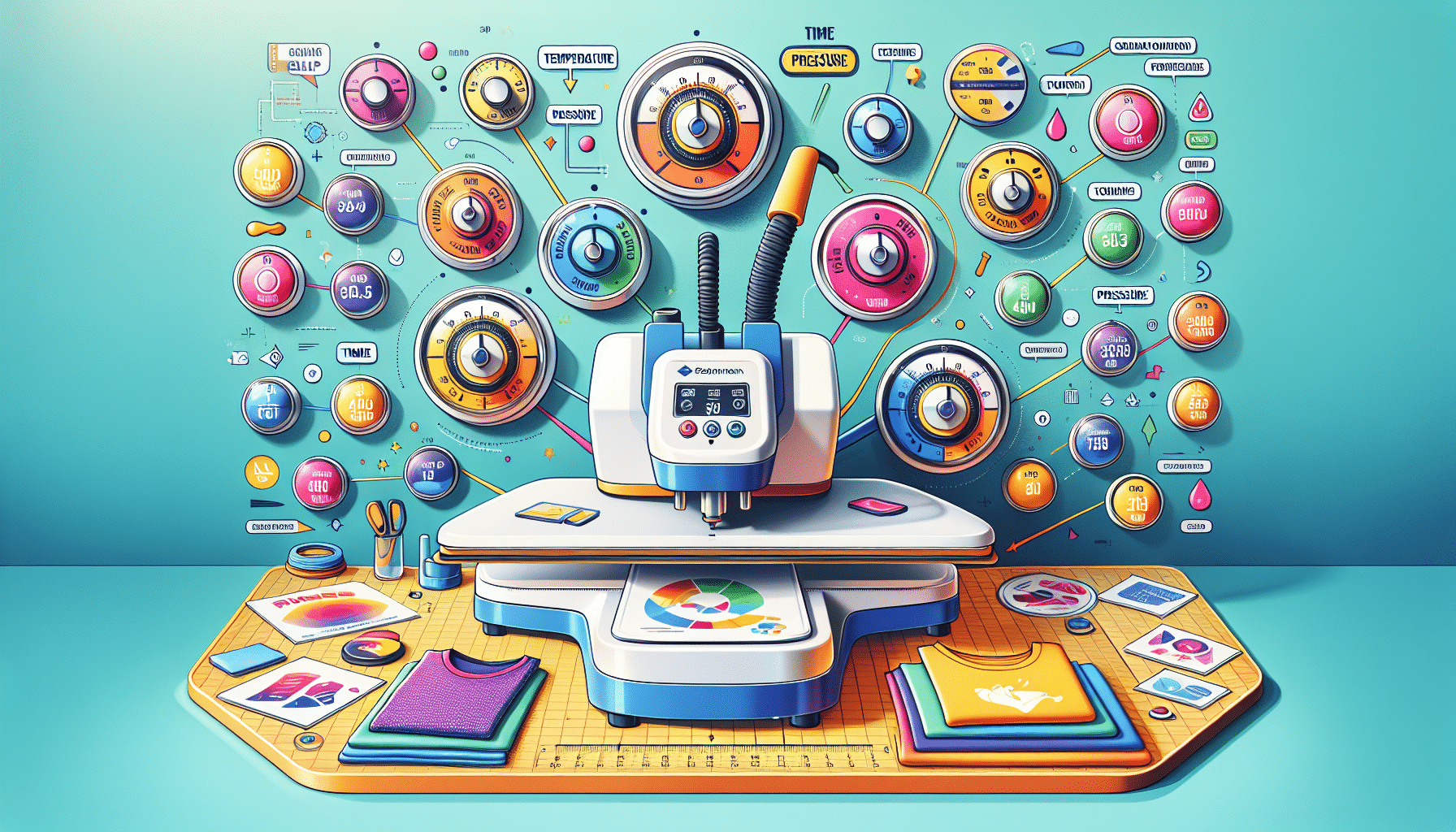
Mastering the fundamental settings of a heat press machine—temperature, time, and pressure—is crucial for effective transfers.
Properly configuring these settings is necessary for methods like dye-sublimation and DTF printing. Settings vary based on fabric type, design size, and other factors, so track and adjust meticulously for consistent results.
Temperature Settings
Correct temperature settings are vital for effective heat transfer and material bonding. Incorrect settings can waste materials and require re-pressing. For HTV, the temperature range is 100°F to 305°F, with specific recommendations for different fabrics.
For example, pressing HTV on cotton fabric requires 380°F, while stretch materials need 335°F. For DTF printing on cotton, a temperature of 320-350°F for 10-15 seconds is suitable. Fine-tuning these settings helps achieve optimal results.
Choosing the correct temperature to avoid yellowing or burning during heat pressing is crucial. A temperature chart can be a handy reference for effective heat press processes.
Time Settings
Pressing time directly influences the effectiveness of heat and pressure application. Insufficient time can result in weak bonds, causing transfers to peel off easily.
For HTV designs, apply pressure for 10-15 seconds. Synthetic fabrics require 2 to 3 seconds, while HTV on cotton needs about 15 minutes. Adjust time settings based on the material for successful transfers.
Pressure Settings
Correct pressure is crucial for effective heat transfer and bonding. Low pressure can cause inadequate adhesion, while excessive pressure may distort or damage fabrics.
For polyester HTV, light pressure is suggested. DTF printing requires heavy pressure to melt adhesive powder and ensure a strong bond. Proper pressure adjustment avoids issues like vinyl peeling or inadequate adhesion.
Comprehensive Heat Press Temperature and Time Chart
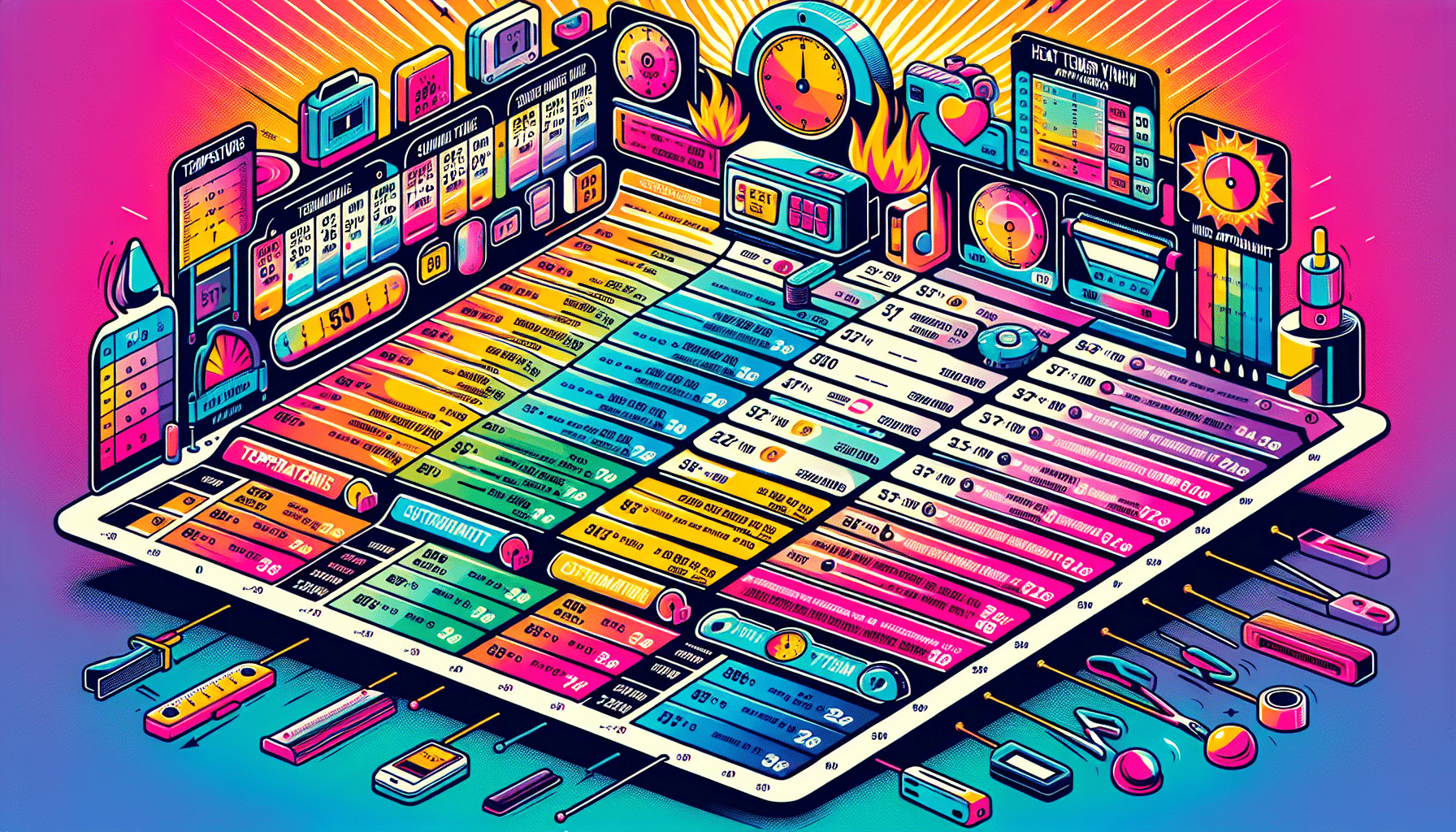
A detailed temperature and time chart is essential for effective heat press processes. These charts offer general recommendations, adjustable based on specific needs and materials.
For instance, the HTVRONT heat press guide includes specific settings for each material, focusing on HTV applications. The HTVRONT Auto Heat Press covers settings for HTV, sublimation paper, and heat transfer paper.
HTV Temperature and Time Guide
The ideal temperature range for HTV is between 260°F to 315°F. HTV glitter requires 350°F for 15 seconds, while printing on cotton fabric needs 356°F.
For polyester HTV, the recommended temperature is 270°F; for synthetic fabrics, it is 302°F. Pressing time for HTV is between 8 to 15 seconds. Different types of HTV may need specific peeling methods for optimal results.
Sublimation Printing Settings
Applying HTVRONT Sublimation HTV to fabric requires specific temperature, duration, and peel methods to ensure print quality. Precise temperature and time settings are crucial for vibrant and durable prints on fabric and other substrates. These settings ensure sublimation ink bonds effectively with polyester or polymer-coated substrates, resulting in high-quality prints.
DTF Printing Settings
DTF printing requires heavy pressure, making it difficult to open the press afterward. Proper temperature and time settings are crucial to ensure the adhesive powder melts and bonds with the fabric effectively.
Adjusting these settings based on DTF printing requirements helps achieve optimal results and ensures high-quality prints.
Tips for Successful Heat Pressing
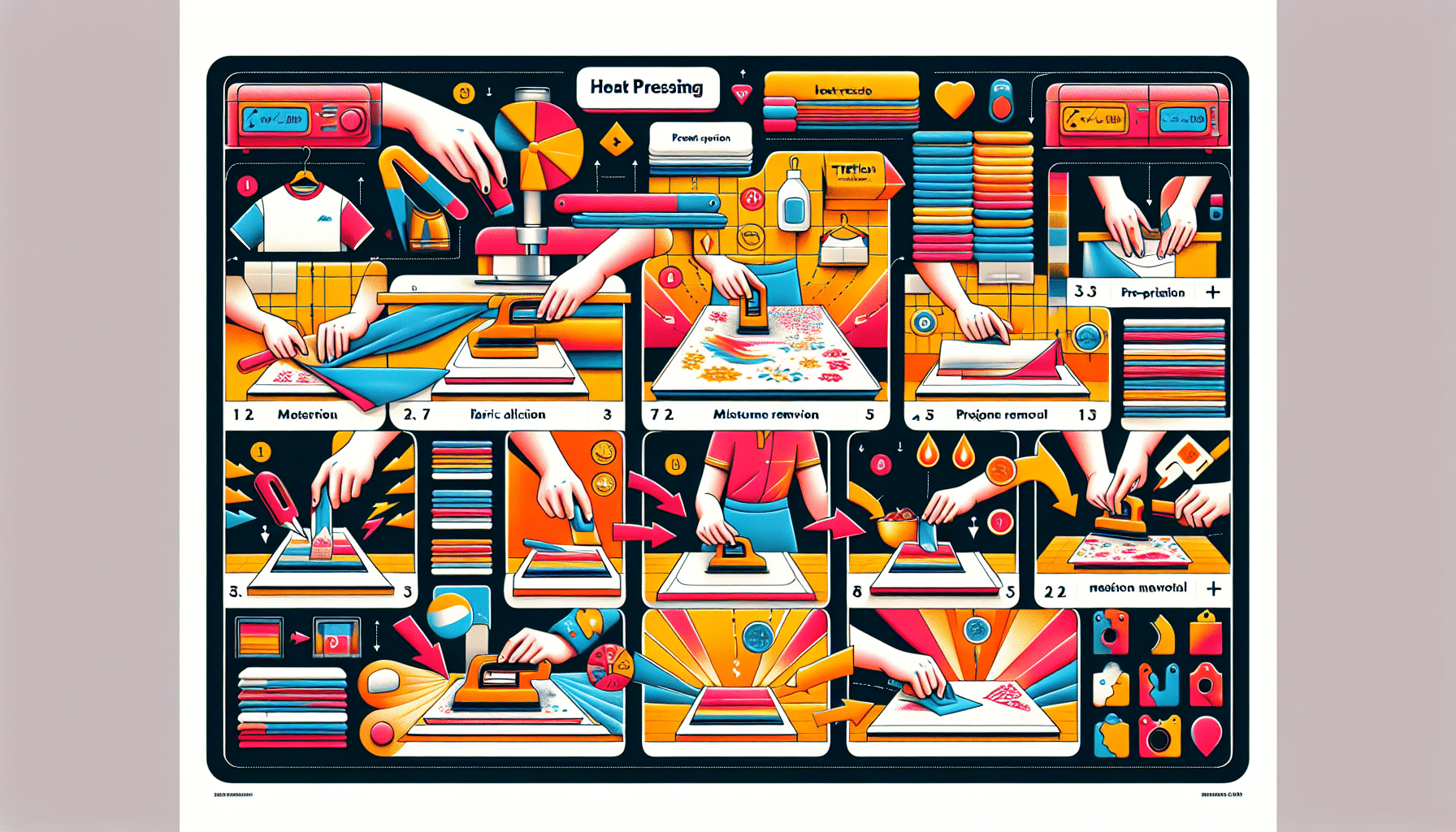
Achieving the best results with a heat press involves more than just setting the correct temperature and heat press time. Practice heat pressing, conduct test runs, and make small adjustments as necessary. Factors like equipment quality, environmental conditions, substrate type, and material quality impact outcomes.
Calibrate heat press settings based on real-time observations and refine techniques through experimentation. This proactive approach helps master heat pressing and consistently produce high-quality results.
Pre-Pressing Techniques
Preheating garments eliminates wrinkles and moisture before designing. This step ensures a smooth and effective transfer, preventing issues like uneven prints or weak adhesion.
Use a heat printing pad or pillow when applying designs near raised areas like collars or seams. These accessories maintain even pressure and prevent distortions in the final print.
Using Teflon Sheets and Parchment Paper
Cover sheets like Teflon or parchment paper protect designs and equipment. They maintain a clean platen and prevent issues like oil stains or improper transfers.
In pre-pressing, placing a Teflon sheet or parchment paper on the garment ensures even heat distribution and protects the design from direct contact with the heat press.
Troubleshooting Common Issues
Common heat pressing problems include peeling vinyl and uneven transfers, often due to variations in materials and machine settings.
Prevent problems by understanding how different materials and settings react. Adjust temperature, time, and pressure settings based on real-time observations to avoid issues like scorching, discoloration, or weak adhesion.
Limitless Transfers
Limitless Transfers excels in the customization industry, awarded first place for quality in DTF printing in 2024. Their transfers are known for superior quality, vibrant colors, and ease of application. With no setup fees, low minimums, and quick turnaround, Limitless Transfers simplifies starting heat press projects.
Orders over $50 qualify for free shipping, and orders placed by noon (EST) ship the same day. Advanced CMYK+W printing technology ensures optimal color accuracy and detail in every transfer. Hot peel transfers enable faster production, ideal for large orders.
For more information, visit Limitless Transfers.
Heat Presses
When it comes to customizing apparel or other items, heat presses are essential tools. They offer precision and efficiency, making them popular among hobbyists and professional designers alike. Here is a list of notable heat presses, each with unique features:
-
Cricut EasyPress: Known for its user-friendly interface and portability, the Cricut EasyPress is ideal for small projects and beginners.
-
PowerPress HPM-1515-BK: This model is celebrated for its durability and even heat and pressure distribution, suitable for heavy-duty projects.
-
Fancierstudio Power Heat Press: With its large platen size, this press is perfect for larger designs and offers great value for money.
-
SENVOZIFF 5 in 1 Heat Press: Offering versatility, this multifunctional heat press can handle a variety of materials, including ceramics and fabrics.
Each of these choices caters to different needs, ensuring that there is an ideal heat press for every project.
Summary
In summary, mastering the correct temperature and time settings for your heat press machine is essential for achieving high-quality results. From understanding the nuances of different heat press applications to troubleshooting common issues, this guide provides all the necessary information to elevate your heat pressing game. Whether you’re working with HTV, sublimation printing, or DTF printing, knowing the ideal settings for your materials will ensure success,.
Remember to always conduct test runs, adjust settings based on real-time observations, and use the right tools and techniques to optimize your heat press outcomes. With the knowledge gained from this guide, you’re now well-equipped to produce flawless transfers and expand your customization capabilities. Happy pressing!
Frequently Asked Questions
What is the recommended temperature for pressing HTV on cotton fabric?
For pressing HTV on cotton fabric, the sweet spot is 380°F. This will ensure a good bond and durability for your design.
How long should I press HTV on synthetic fabrics?
When working with synthetic fabrics, you should press HTV for about 2 to 3 seconds. This quick heat should keep your material safe while ensuring a secure bond!
What pressure setting should I use for DTF printing?
For DTF printing, you should use a heavy pressure setting to effectively melt the adhesive powder and create a strong bond with the fabric.
Why is preheating garments important before heat pressing?
Preheating garments is essential because it helps remove wrinkles and moisture, making sure the heat transfer goes on smoothly and effectively. This simple step can make a big difference in the final result!
What are the benefits of using Teflon sheets or parchment paper during heat pressing?
Using Teflon sheets or parchment paper during heat pressing is a game-changer—they protect your designs and equipment while keeping your platen clean and ensuring even heat distribution. It’s a simple step that leads to a much better result